What is Tooling?
Tooling, often referred to as molds, is a critical component in the manufacturing process. It involves the creation of a precise cavity or negative space into which molten plastic resin is injected to form parts. To ensure the production of high-quantity and high-quality components, it is essential to invest in well-designed and meticulously constructed tooling. Given the complexity of tool design and fabrication, significant capital investment and ample lead time are required to develop effective molds that meet the desired specifications and production standards.
Mold Types
Liquid Silicone Rubber (LSR) Molds
- Liquid Injection Molding: A precise and efficient molding process tailored for LSR.
- Hot Runner System: Ensures consistent flow and temperature control.
- Cold Runner System: Ideal for minimizing material waste and improving cycle times.
- Open Tip Nozzle: Designed for direct material injection with precision.
- Valve Gated Nozzle: Provides enhanced control over the injection process, reducing material leakage.
- Side Actuated Inserts: Allow for complex part geometries with undercuts.
- Automated Demolding Systems: Utilize sweeps and robots for efficient, hands-free part removal.
High-Consistency Rubber (HCR) Mold
- Compression Molding: Traditional method for creating durable HCR parts.
- Injection Molding: Combines speed with accuracy, ideal for high-volume production.
- Transfer Molding: Offers versatility, especially for intricate designs.
- Flashless/Wasteless Molding: Eliminates excess material, producing clean parts without additional trimming.
- Self-Registered Inserts: Ensures precise alignment within the mold cavity.
- Cut-in-Plate Design: Optimizes material flow and reduces waste.
- Hybrid Molds: Combines inserts and cut-in-plate techniques for enhanced versatility.
- Split Bar: Facilitates easy demolding of complex shapes.
- Accordion Bar: Allows for flexibility in part design, accommodating intricate details and varying thicknesses.
Tooling Production Process
1. CAD Design: The tooling process begins with a detailed Computer-Aided Design (CAD) model. This digital blueprint defines every aspect of the mold, including dimensions, geometry, and the required tolerances. The design stage is crucial as it lays the foundation for precision and functionality in the final tool.
2. Mold Base and Accessories: Following the CAD design, the mold base and essential components such as guide pins, bushings, and clamping plates are selected. These elements form the structural backbone of the mold, ensuring stability and alignment during the molding process.
3. Rough Machining: Once the base is prepared, rough machining begins. This involves removing excess material from the mold blocks to create a basic shape that approximates the final design. This step uses heavy-duty milling machines and lathes to carve out the general contours of the tool.
4. Heat Treatment: After rough machining, the tool undergoes heat treatment to enhance its hardness and durability. This process involves heating the metal to a high temperature and then cooling it under controlled conditions. Heat treatment is essential for extending the lifespan of the tool, particularly in high-volume production environments.
5. CNC Precision Machining: Following heat treatment, the tool undergoes CNC (Computer Numerical Control) precision machining. This step refines the tool's features with high accuracy, ensuring that every dimension and surface finish meets the exact specifications outlined in the CAD design. CNC machining is vital for achieving the intricate details and tight tolerances required for high-quality mold production.
6. Hard Milling: The final machining process involves hard milling, where the tool's surfaces are further refined to achieve the desired finish. This step ensures that the tool is not only functional but also has a smooth and polished surface, which is critical for producing parts with high cosmetic standards.


Considerations for Tool Design
Designing effective tooling requires careful consideration of several factors, including complexity, expected lifespan, application, and production volume. Deciding on the appropriate tooling investment is a crucial decision in the manufacturing process. For projects that will transition directly into high-volume production, investing in high-quality, durable production tooling is typically the most cost-effective strategy in the long run. Conversely, for low-volume production runs, starting with a prototype tool may be more advantageous until production volumes justify a more significant investment.
Neosilicone plays a vital role in the tool design process, leveraging our expertise in fabrication techniques and tooling design. We perform mold flow analyses to refine the tooling design, optimizing the placement of parting lines, gates, and ejection points. Our skilled prototype design engineer collaborates closely with toolmakers to ensure the development of the most effective tool for the specific application.
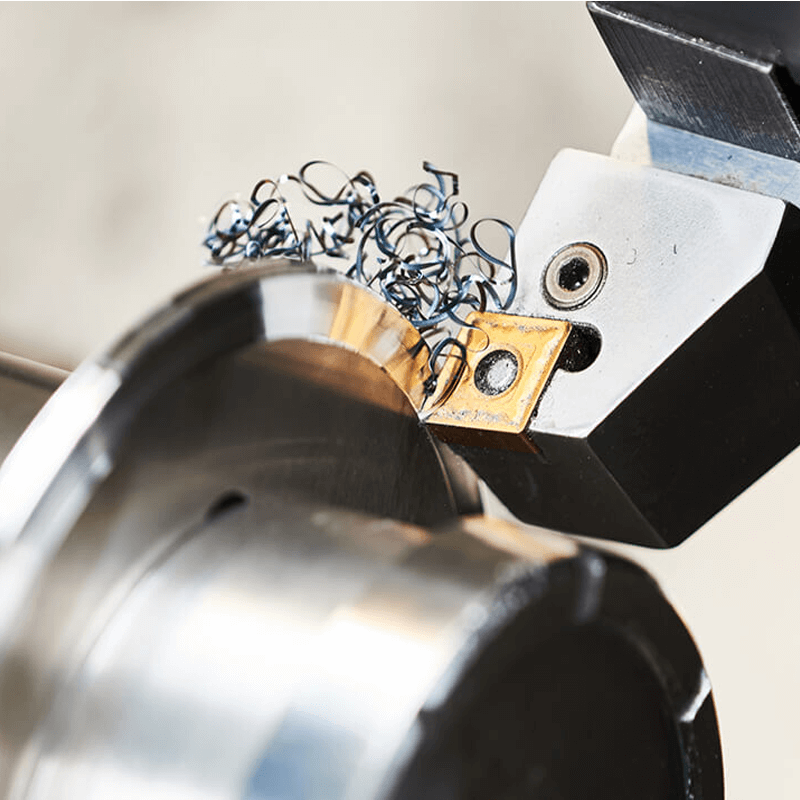
Why Choose Us for Your Tooling and Mold Design
1. Customized Engineering Solutions: We provide tailored tooling and mold design services that meet the unique specifications of your project, ensuring that every tool is optimized for efficiency and performance.
2. Advanced Simulation and Analysis: Our team employs cutting-edge mold flow analysis and finite element analysis (FEA) to predict potential issues before production, reducing risk and improving overall tool quality.
3. Precision Manufacturing Capabilities: With state-of-the-art CNC machining and advanced milling technologies, we deliver tooling with unparalleled accuracy, enhancing the consistency and quality of your molded parts.
4. State-of-the-Art Technology and Equipment:We leverage top-tier technology and an extensive range of advanced machinery to deliver superior tooling solutions. Our facility is equipped with high-precision CNC machines, EDM (Electrical Discharge Machining) systems, surface grinders, and advanced heat treatment furnaces, all critical for producing high-quality tools with exacting standards.
Applications
1. Automotive Industry: Precision tooling and mold design are essential for producing complex components such as engine parts, interior trims, and safety features, ensuring high-quality, reliable performance in vehicles.
2. Medical Devices: In the medical sector, tooling and mold design are critical for manufacturing sterile, high-precision components like surgical instruments, diagnostic devices, and implantable parts, where accuracy and quality are paramount.
3. Consumer Electronics: The consumer electronics industry relies on advanced tooling and mold design to create intricate, durable components for devices such as smartphones, laptops, and wearable technology, balancing aesthetics with functionality.
4. Aerospace and Defense: This industry demands exceptional precision and durability in tooling and mold design for producing high-performance components used in aircraft, satellites, and defense systems, where safety and reliability are non-negotiable.