About Overmolding
Overmolding is a sophisticated injection molding technique that integrates two or more distinct materials into a single, unified product. Typically, this process involves covering a rigid base substrate with a flexible, rubber-like layer, such as a thermoplastic elastomer (TPE).
As the pinnacle of multi-material injection molding, overmolding allows for the seamless fusion of different materials, resulting in enhanced product design, functionality, and visual appeal. The process uses multiple molding machines: one to create the initial substrate and another to apply a thin TPE layer over it. The outcome is a highly adaptable, application-specific solution, ideal for manufacturers across various industries, including those specializing in silicone products.
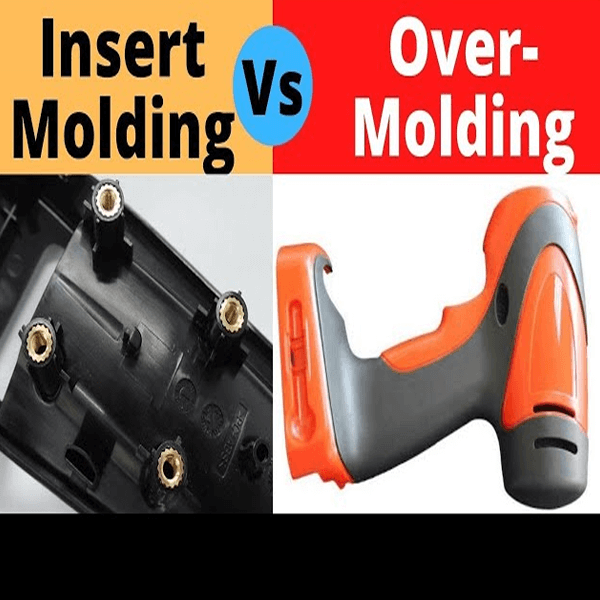
Overmolding vs. Insert Molding
Expert injection molders like Neosilicone offer a wide range of services, including both overmolding and insert molding, two techniques that, while similar, have key distinctions.
Insert molding involves creating specialized tooling designed to securely hold a solid component—referred to as the insert—within another mold. Thermoplastic or TPE material is then injected into the mold, encasing the insert and producing a finished part.
The insert itself can be a single piece or a combination of individual components meticulously arranged within the mold, which are then bonded together by the injected plastic. This method can enhance the overall strength, flexibility, and functionality of the final product compared to assembling parts separately in post-production. Insert molding often reduces or even eliminates the need for secondary assembly steps, thereby saving time and lowering production costs.
Neosilicone’s advanced automation technology, coupled with both horizontal and vertical insert molding machines, significantly reduces human error, boosts efficiency, and ensures optimal results in the production of silicone products.
Advantages of Overmolding
Overmolding offers numerous benefits that go beyond eliminating assembly steps, adding significant value to silicone products that end-users seek and expect:
- Reduced Shock and Vibration: Overmolding provides enhanced impact resistance, making products more durable and long-lasting.
- Effective Sealing: It creates strong oxygen and moisture barriers, ensuring superior sealing performance.
- Sound Dampening: Overmolding effectively reduces noise, making products quieter in operation.
- Electrical Insulation: It offers excellent electrical insulation properties, vital for electronic applications.
- Enhanced Resistance: Products gain improved chemical and UV resistance, extending their lifespan.
- Aesthetic Appeal: Overmolding allows for a wide range of vibrant, visually appealing exterior finishes.
For OEMs, overmolding is a cost-effective production method because it:
- Streamlines Production: Eliminates additional injection molding steps required for assembling individual components.
- Enhances Bonding: Creates a strong bond between the substrate and TPE, removing the need for downstream finishing processes like priming, painting, or coating.
- Increases Efficiency: Improves product quality and throughput while minimizing waste.
In addition to cost savings, overmolding also accelerates time-to-market, providing OEMs with a competitive edge by delivering high-quality silicone products faster.
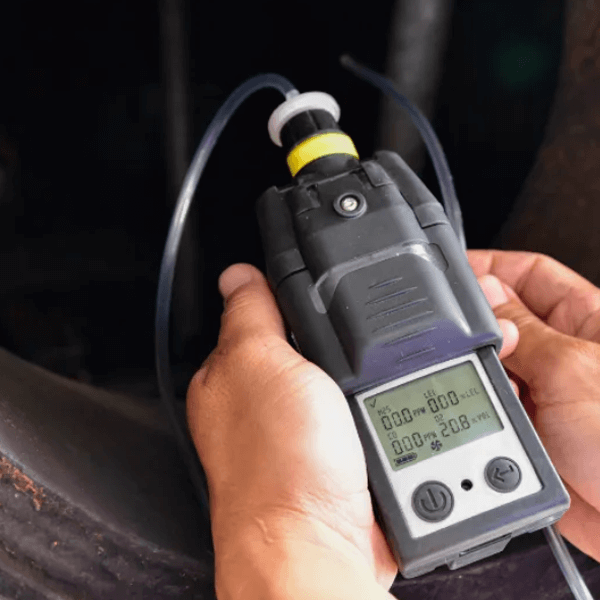
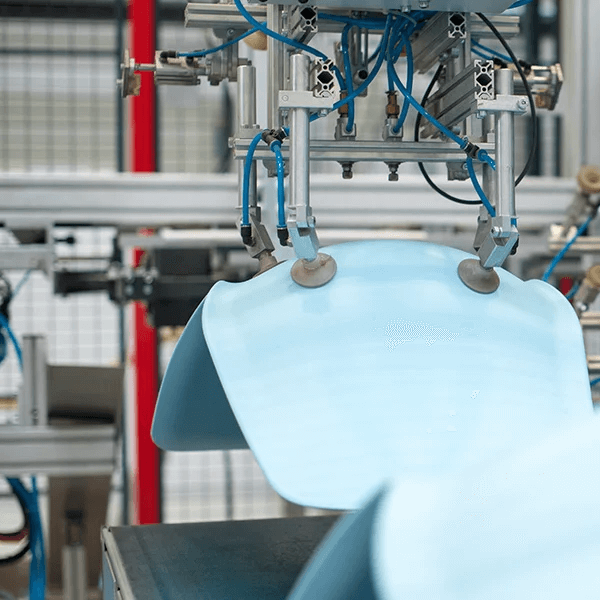
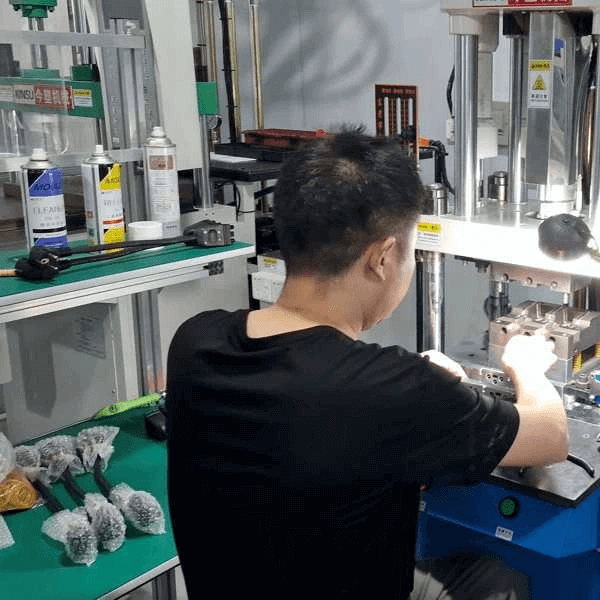
Overmolding Materials and Design
For engineers and designers, one of the most significant advantages of overmolding is the enhanced "touch" or "feel" it imparts to silicone products. However, achieving the desired tactile qualities in overmolding design requires careful consideration of several interacting factors, including:
- Friction Coefficient: Affects the grip and slip resistance of the finished product.
- Hardness: Determines the durability and resistance to deformation.
- Thickness: The thickness of the TPE layer plays a critical role in the perceived softness, with thinner layers feeling firmer despite the material’s inherent pliability.
The challenge lies in balancing these factors to achieve the desired outcome. For example, even with a highly flexible resin, a thin TPE layer will feel firmer because the overall softness is more influenced by the layer's thickness than by the material's inherent softness.
Advancements in TPE formulations continue to expand the possibilities for bonding high-performance thermoplastic resins to rigid plastic substrates. This is crucial because not all substrates and TPEs are compatible. Adhering to compatibility guidelines in the overmolding design process is essential for successful results.
Compatible overmolding substrates include:
- Polypropylene
- Copolyester
- Polystyrenes
- Polycarbonate (PC)
- Acrylonitrile Butadiene Styrene (ABS)
- Polycarbonate ABS (PC-ABS)
- Polymethyl Methacrylate (PMMA)
- High-Density Polyethylene (HDPE)
- Standard and Modified Nylon 6
- Polyphenylene Oxide (PPO)
When it comes to plastic over metal substrates, the materials are generally compatible, with minimal chemical limitations. This compatibility ensures that silicone products consistently meet their intended performance requirements, offering reliability and durability across various applications.
Overmolding Applications
Overmolding is a highly versatile process, making it a popular choice across various industries due to its multifaceted benefits.
In some applications, overmolding serves an aesthetic function by adding contrasting colors or textures. It can also enhance functionality, such as improving grip on consumer products like toothbrushes.
However, overmolding is often crucial for ensuring health, safety, and performance, particularly in industries where durability and protection are paramount. Notable applications include:
1. Medical Industry: Overmolding is essential for medical devices and equipment. It ensures that surgical instruments and medical suite components remain sterile, durable, and capable of withstanding exposure to harsh chemicals and rigorous medical environments.
2. Automotive Industry: In automotive applications, overmolding provides crucial weatherproofing for electrical components, such as outdoor outlet covers and automotive wiring assemblies, which are exposed to harsh environmental conditions.
3. Defense Sector: Overmolding enhances the durability of handheld navigation and communication devices used by emergency and military personnel. These devices must withstand extreme conditions and rough handling, making overmolding a vital element for their protection and reliability.
4. Consumer Electronics: Overmolding is widely used in consumer electronics to enhance ergonomics and protect sensitive components. For example, it is applied to enhance the grip and durability of smartphone cases, as well as to provide additional shock absorption for electronic devices subjected to frequent handling.
By integrating overmolding into these applications, manufacturers can achieve both functional and aesthetic improvements, enhancing product performance and user experience across a diverse range of industries.
Overmolding Expertise
Overmolding is a specialized process that not all injection molders can execute effectively. It demands not only advanced equipment but also rigorous training, a thorough understanding of scientific molding principles, and precise management of multiple variables throughout the production cycle.
Due to the complexity of the process, even minor deviations can significantly impact product quality. Therefore, it is crucial to have skilled injection molding engineers, technicians, and operators who are adept at establishing optimal process parameters and overseeing in-tool conditions throughout the overmolding process.
Manufacturers that partner with injection molding experts, such as Neosilicone, gain access to specialized overmolding capabilities. These partnerships ensure that the benefits of overmolding—such as high-quality, visually appealing products produced at reduced costs—are fully realized. By leveraging the expertise of experienced professionals, companies can achieve superior results in their overmolding projects.