About Silicone Extrusion Molding
Silicone extrusion is a highly efficient and cost-effective continuous molding technique that enables rapid production of high-volume silicone products. In this process, silicone material is subjected to thermal curing within specialized molds and equipment, resulting in the formation of precise cross-sections, intricate contours, and continuous lengths.
This method is particularly well-suited for manufacturing silicone products with unrestricted tubular or strip shapes. It is commonly used to produce items such as medical silicone tubing, silicone wires, sealing strips, gaskets, and other complex geometries. The extrusion process delivers consistent quality and high production rates, making it an ideal choice for a broad range of silicone applications.
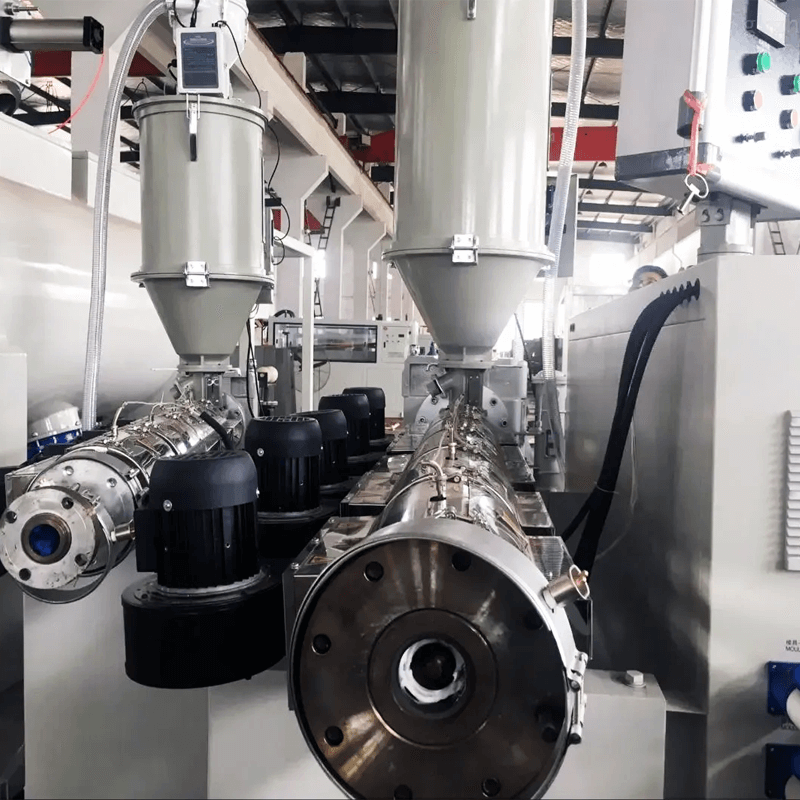
The Production Process of Silicone Extrusion Molding
1. Material Preparation: The process begins with the preparation of pretreated silicone raw material, which is formulated and conditioned to meet specific production requirements. This preparation ensures that the silicone possesses the necessary properties for optimal extrusion.
2. Extrusion: The silicone material is fed into the extrusion machine, where it is subjected to high temperatures and pressures. The extrusion machine, equipped with a specialized die and extruder head, shapes the silicone into a continuous strip or profile. The die determines the final cross-sectional shape of the product, while the extruder head ensures uniform flow and consistency.
3. Curing: Once extruded, the silicone strip undergoes a series of post-extrusion treatments. The continuous strip is repeatedly pulled through a series of heating zones to achieve curing. This step ensures that the silicone solidifies and attains the desired mechanical properties, such as elasticity and durability.
4. Cutting and Finishing: After curing, the silicone strip is cut into specified lengths or shapes according to customer requirements. The flexibility of the extrusion process allows for the production of various forms, including plates, tubes, and strips. These finished products can be customized further based on application needs.
5. Quality Control: Stringent quality control measures are implemented throughout the extrusion process. This includes monitoring the extrusion parameters, ensuring consistent product dimensions, and verifying that the cured silicone meets industry standards for performance and safety.
Silicone extrusion molding is advantageous for producing high-volume, uniformly shaped silicone products. Its efficiency and versatility make it ideal for applications in medical devices, food machinery, and other sectors where precision and consistency are crucial. The ability to cut and shape the extruded silicone post-production further enhances its adaptability for various uses.
Advantages of Silicone Extrusion Molding
1. Consistent Quality: The extrusion process ensures uniformity and density in silicone products through the continuous mixing and plasticizing of the material by the rotating extruder screw. This results in a consistently high-quality output with improved material integrity.
2. High Production Efficiency: The extrusion process is characterized by its rapid molding capabilities, leading to high production rates. This efficiency is particularly advantageous for high-volume manufacturing and automated production environments.
3. Customizable Length: Extrusion molding allows for the production of silicone products in virtually unlimited lengths. This flexibility ensures that products can be tailored to specific customer needs without constraints on length.
4. Material Flexibility: A wide variety of silicone materials can be used in extrusion molding, including options for different calibers, colors, translucency, hardness, and precision grades. This customization capability enables the production of silicone products that meet precise specifications and performance criteria.


Why Choose Neosilicone for Your Silicone Extrusion Needs
1. Tailored Extrusion Services: Neosilicone offers customized silicone extrusion molding solutions, accommodating various collaboration models including wholesale, OEM, and contract manufacturing. We tailor our services to meet your specific requirements and project goals.
2. Comprehensive Capabilities: Our expertise spans the entire extrusion process, from part design and material selection to performance testing and prototyping. We also provide custom mold creation, full-scale product manufacturing, and additional value-added services to support your project at every stage.
3. Efficient Production Lines: With multiple, high-performance extrusion molding production lines, we ensure that your projects are completed efficiently and cost-effectively. Our advanced production capabilities help you meet your business objectives while optimizing cost and turnaround time.
4. Quality Assurance: Our facility is ISO 9001:2015 certified, guaranteeing adherence to rigorous quality standards. This certification provides assurance of our commitment to maintaining superior quality throughout the production process.
5. Extensive Experience: With over a decade of expertise in silicone extrusion molding, Neosilicone brings valuable industry knowledge and experience to every project. Our seasoned professionals are equipped to handle complex extrusion requirements with precision and reliability.
6. Precision Control: We maintain stringent process control to achieve the precise properties and dimensions required in silicone extrusion. Our meticulous approach ensures that each product meets your exact specifications and performance criteria.
Available Equipment for Silicone Extrusion Molding
1. Silicone Extruder Machines: Precision-engineered extruders designed to process silicone materials with high accuracy and efficiency, facilitating the production of consistent and high-quality extruded profiles.
2. Silicone Curing Systems: Advanced curing equipment that ensures the complete vulcanization of silicone products, maintaining optimal properties and dimensional stability through controlled temperature and pressure conditions.
3. Smooth Bore Extruders: Specialized extruders equipped with smooth bore technology to produce flawless, uniform silicone profiles, minimizing surface imperfections and ensuring high-quality output.
4. Electrical Control Systems and Line Integration: Sophisticated control systems that manage the extrusion process, including temperature regulation, pressure control, and synchronization of various production stages for seamless operation.
5. Extension Tunnels: Integrated tunnels that facilitate the cooling and further processing of extruded silicone products, ensuring proper curing and stabilization of the material as it exits the extruder.
6. High-Speed Cutters and Cooling Units: Precision cutting tools and cooling systems designed to efficiently trim and cool extruded silicone products, maintaining product integrity and enhancing overall production efficiency.
Applications of Silicone Extrusion Molding
1. Medical and Healthcare: Silicone extrusion molding is extensively used to produce medical-grade silicone tubing, gaskets, and seals. These products are critical in healthcare applications due to their biocompatibility, flexibility, and resistance to sterilization processes. Common applications include medical device components, respiratory tubes, and catheters.
2. Food and Beverage Industry: In the food and beverage sector, silicone extrusion molding is employed to manufacture various components such as seals, gaskets, and tubing. Silicone’s non-reactive and temperature-resistant properties make it ideal for applications involving food contact and high-temperature environments, ensuring safety and durability.
3. Automotive Industry: Extruded silicone products are used in the automotive sector for seals, gaskets, and tubing. The high-performance characteristics of silicone, including its resistance to extreme temperatures and environmental factors, make it suitable for automotive applications that require reliable sealing and protection.
4. Consumer Goods: In consumer products, silicone extrusion molding is used to create a wide range of items such as kitchenware, sports equipment, and personal care items. The versatility of silicone allows for the production of durable, flexible, and aesthetically diverse products that meet various functional and design requirements.