Plastic Injection Molding Manufacturer
We specialize in providing comprehensive injection molding services, offering capabilities ranging from 75 to 320 tons. Our expertise encompasses rapid prototyping, manufacturing high-quality products, and producing large-scale parts. Our experienced design and engineering teams excel at delivering professional solutions promptly after conducting a thorough evaluation of product designs. We guarantee the delivery of premium molds within 20-35 days.
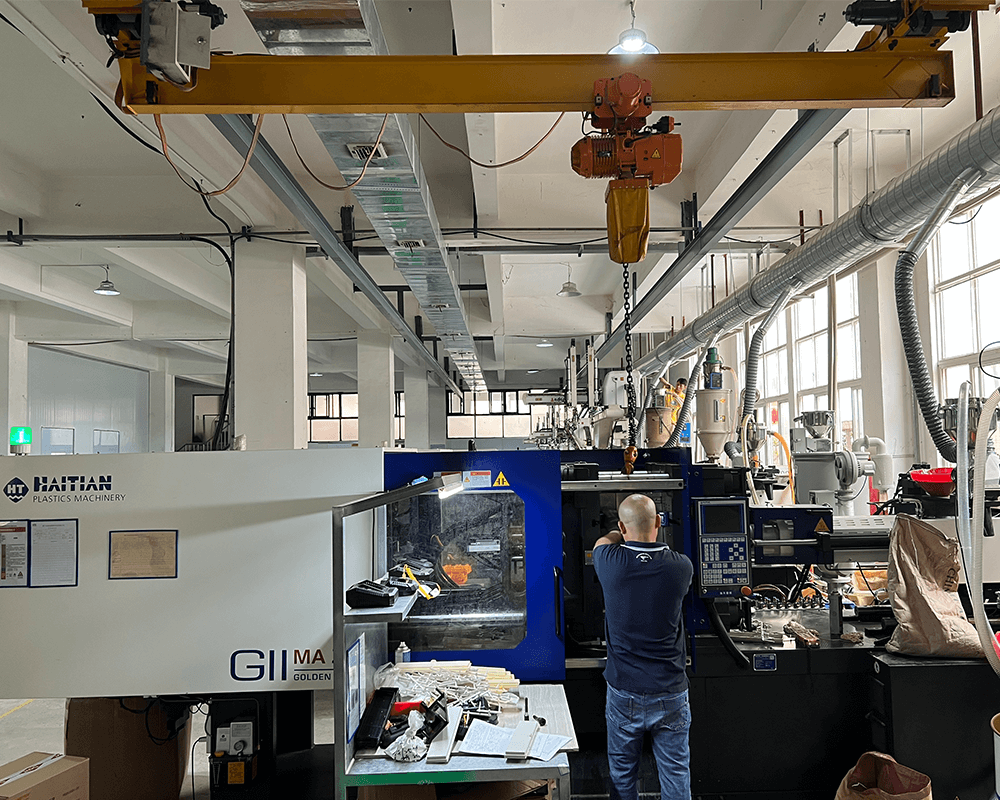
Plastic Injection Molding Capabilities
Injection molding
The injection molding process accommodates a diverse array of resin materials. The plastic resin is heated to high temperatures until molten, then injected into a pre-designed metal mold. As the resin cools and hardens, it adopts the mold's shape, forming the desired component. Our engineers will provide a range of raw material options customized to meet your specific needs.
Overmolding
Overmolding seamlessly combines multiple materials into a single component, enhancing product features such as UV resistance, chemical resistance, and impact resistance. This process also eliminates the additional costs associated with assembly. Due to the varying shrinkage rates of different materials, achieving precise mold accuracy is especially critical.
Insert molding
The mechanical properties of the component are enhanced through insert molding, wherein a preformed part is inserted into a mold and subsequently overmolded with plastic to form a unified component. This eliminates the need for additional components to connect various parts, thereby enhancing assembly efficiency and reducing associated costs.
Precision Molding
Precision molding focuses on producing components with intricate details and tight tolerances. This capability is essential for industries requiring high accuracy, such as medical devices, electronics, and automotive parts. By leveraging advanced mold design and precise injection techniques, we deliver consistent, high-quality parts that meet exact specifications.
Our Plastic Injection Molding Advantages
We offer comprehensive injection molding services to global suppliers. Our team of skilled and diverse designers and engineers provides cost-effective solutions. Our robust management system ensures the delivery of reliable, high-quality products, meeting your need for quick turnaround times.
Outstanding Quality
Our organizational structure and management system are designed for excellence. All raw materials undergo stringent quality assurance, as our procurement team meticulously reviews their quality. We deliver high-quality products and exceptional service to our customers.
Fast Turnaround
Our professional team offers convenient and expedited custom services. From product design and DFM review to prototyping, our process takes only 10-15 days. We also provide a transparent production process and samples for your reference, ensuring you achieve your ideal product effortlessly.
Extensive Use
We can produce injection parts from nearly 200 different thermoplastic resins. We can achieve varied colors and hardness by integrating multiple materials into a single component through two-shot molding, overmolding, and insert molding. Our products are widely used in household, medical, electronic, and industrial applications.
Cost-effectiveness
We offer comprehensive custom services at competitive prices. With over 20 injection machines, we can meet all your production needs. A single high-precision mold can produce hundreds of thousands of parts. Even in mass production, we ensure the consistency of each part.
Surface Finish Options
Draft angle requirements will vary by the requested finish. Industry-standard Mold-Tech finishes are also available.
FINISH | DESCRIPTION |
PM-F0 | non-cosmetic, finish to Protolabs' discretion |
PM-F1 | low-cosmetic, most tool marks removed |
PM-F2 | non-cosmetic, EDM permissible |
SPI-C1 | 600 grit stone, 10-12 Ra |
PM-T1 | SPI-C1 + light bead blast |
PM-T2 | SPI-C1 + medium bead blast |
SPI-B1 | 600 grit paper, 2-3 Ra |
SPI-A2 | grade #2 diamond buff, 1-2 Ra |
Plastic Injection Molding Process
We specialize in providing high-precision and complex plastic parts in a shorter time. The plastic injection molding process is straightforward and efficient, capable of producing custom prototypes and end-use production parts within 15 days. The injection machine consists of three main parts: the mold, the injection unit, and the clamping unit. Here are the steps to customize your plastic products through the plastic injection molding process:
Step 1: Injection Molding
Thermoplastic resins are loaded into the injection machine barrel by our operators. They undergo melting, compression, and injection into the mold under predetermined conditions.
Step 2: Demolding
Thermoplastic resins cure in the mold. After the thermoplastic materials are cooled, the parts are demolded. Once demolding is complete, the finished parts fall into a loading bin.
Step 3: Deflashing
Our quality control team meticulously inspects each product, using a testing machine to identify any rough edges. These edges are then trimmed off, ensuring the plastic products are clean and neat.
Step 4: Final Inspection & Packaging
Each part undergoes a final inspection to ensure it meets the required quality standards. Once approved, the products are carefully packaged, ready for shipment to ensure they arrive in perfect condition.
FAQs
Q: How Much Does Plastic Injection Molding Cost?
A: Discover how to reduce the manufacturing costs of your custom parts through our injection molding guide, which explores the key factors influencing expenses such as tooling, materials, and production.
Q: Who Owns the Injection Mold?
A: Customers own all custom tooling they develop, while reusable proprietary components created by the manufacturing partner (MP) become the MP's property. Custom tooling remains at the MP's facility for a minimum of two years, with the option for extension if needed. Transfers to other locations are possible at the requester's expense.
Q; What Is the Process After Ordering?
A: Upon receiving the order, our manufacturing engineers review the statement of work. A case manager is assigned, and a suitable manufacturing supplier is selected. We create a thorough DFM report for approval. After approval, tooling and mold production begin. T1 samples are produced and sent for approval. Upon approval, the rest of the parts are manufactured.
Q: What ISO Certifications Do You Have?
A: Having both ISO 9001 and IATF 16949 certifications showcases our dedication to maintaining rigorous quality management practices and meeting the stringent requirements of our client’s industry.